Staying competitive in the manufacturing industry demands technology integration into every facet of production. Yes, this includes automation and artificial intelligence, but let’s not forget good old-fashioned IT support. So, what does IT support for manufacturing really look like? Is it a nice-to-have or an absolute necessity? And most importantly, should you build your own IT support team or rely on outsourcing?
Recent data shows that 37% of businesses outsource IT at least partly, while others increasingly consider dedicated in-house teams tailored to their specific needs. This decision is especially critical in manufacturing, where even a minor system glitch can lead to costly downtime.
In this post, we’ll break down everything you need to know about IT support for manufacturing, including:
- What IT support for manufacturing entails.
- The key reasons the manufacturing industry benefits from IT support.
- How to choose the right IT support system for your business.
Let’s dive in!
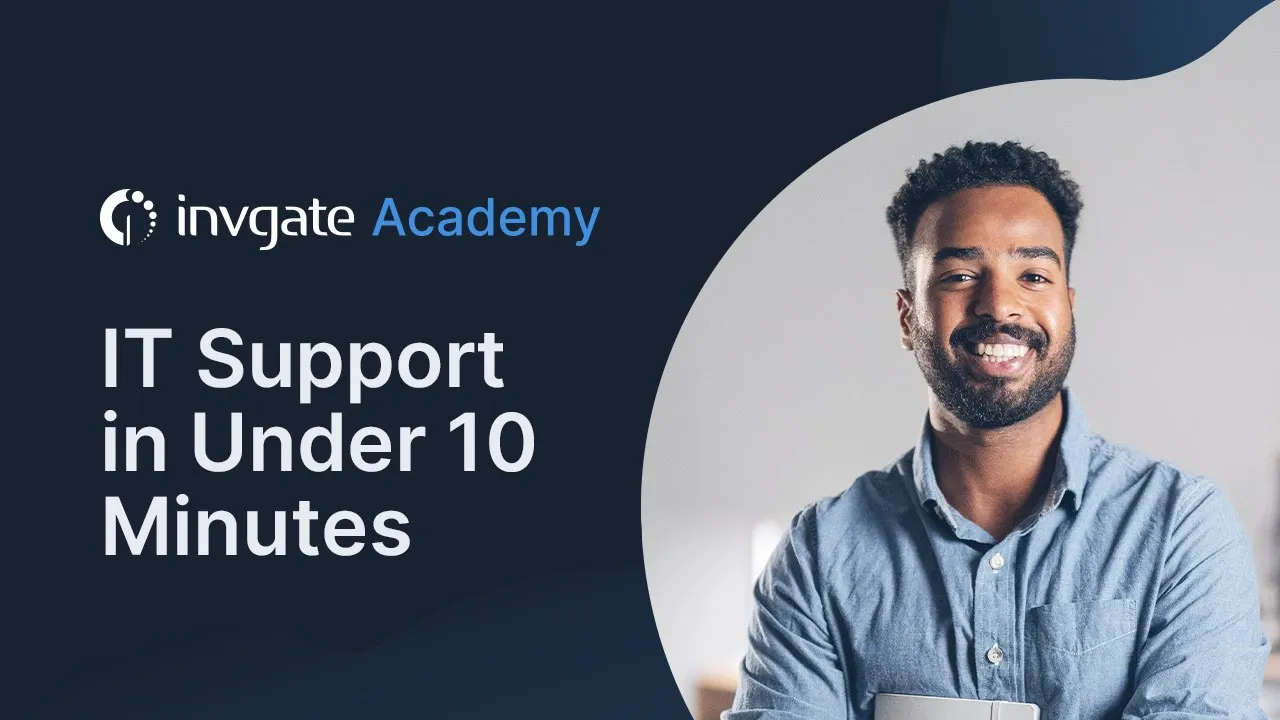
What is IT support for manufacturing?
IT support for manufacturing focuses on maintaining the technology that keeps production running smoothly. It covers both traditional IT systems —like networks, servers, and business applications— and specialized manufacturing technologies, such as industrial control systems and automation software.
IT teams in this sector manage enterprise resource planning (ERP) software, supply chain management tools, and factory-floor systems that monitor production. They ensure these applications run efficiently, assist employees with technical issues, and handle software updates. Cybersecurity is also a key responsibility, protecting factory networks and sensitive data from cyber threats.
Beyond software, IT support maintains the hardware that connects manufacturing processes. This includes industrial PCs, sensors, and connected devices used in smart factories. IT teams also help integrate these technologies with business systems, enabling real-time monitoring and data analysis to improve efficiency and prevent disruptions.
In short, IT support in manufacturing keeps both office and production technologies working together, minimizing downtime, improving security, and helping businesses adapt to technological advancements.
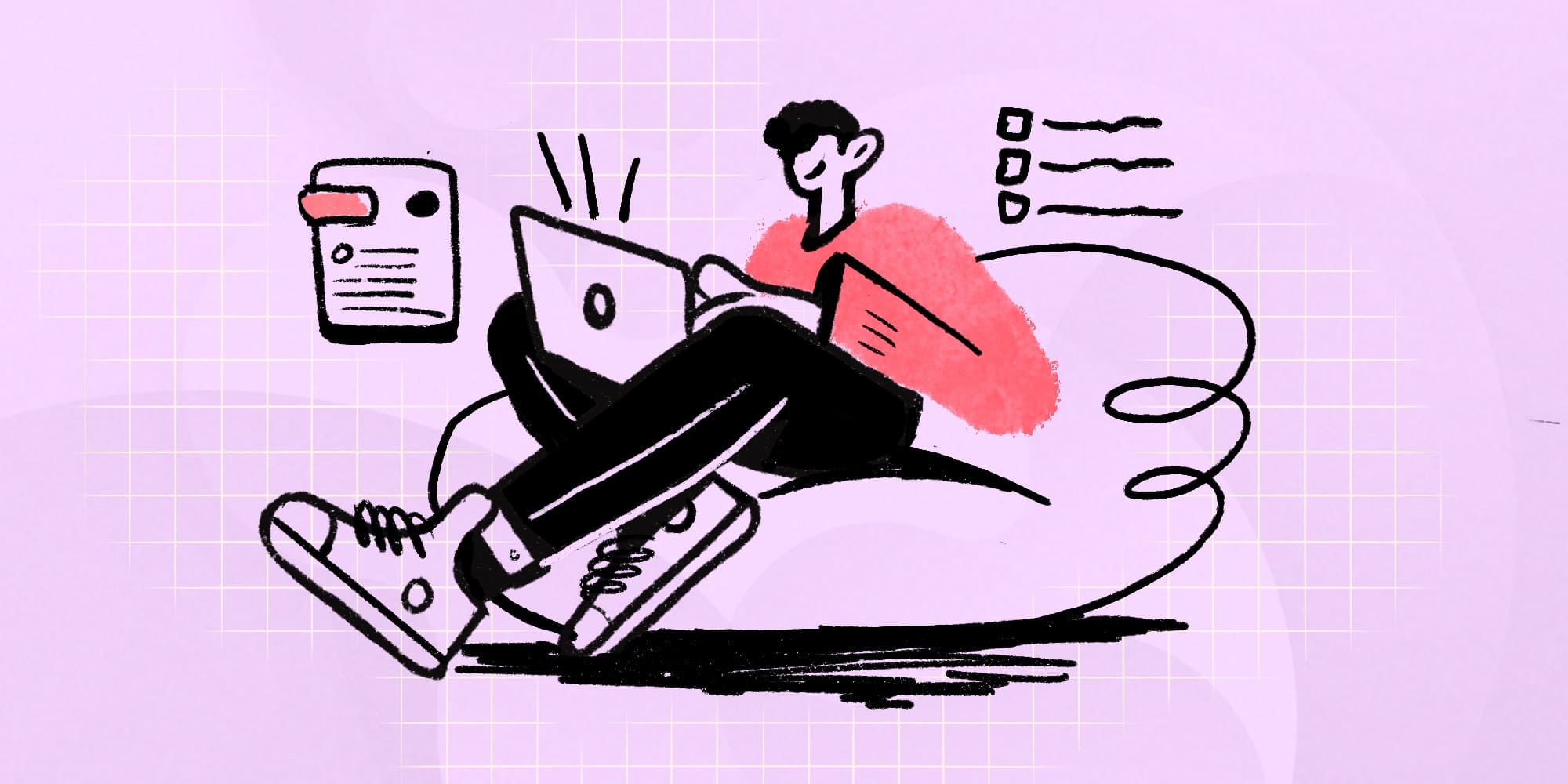
Outsourced vs. in-house IT support for manufacturing
Manufacturing companies can either manage IT support internally or outsource it to a third-party provider. The right choice depends on budget, operational complexity, and security needs.
Outsourced IT support provides access to a broader range of expertise and 24/7 monitoring, often at a lower cost than maintaining a full in-house team. However, response times may be slower, and external providers might not fully understand the nuances of a specific manufacturing environment.
In-house IT support offers direct control over IT operations, faster on-site issue resolution, and better alignment with company-specific processes. The drawback is the higher cost of maintaining a skilled team and investing in infrastructure.
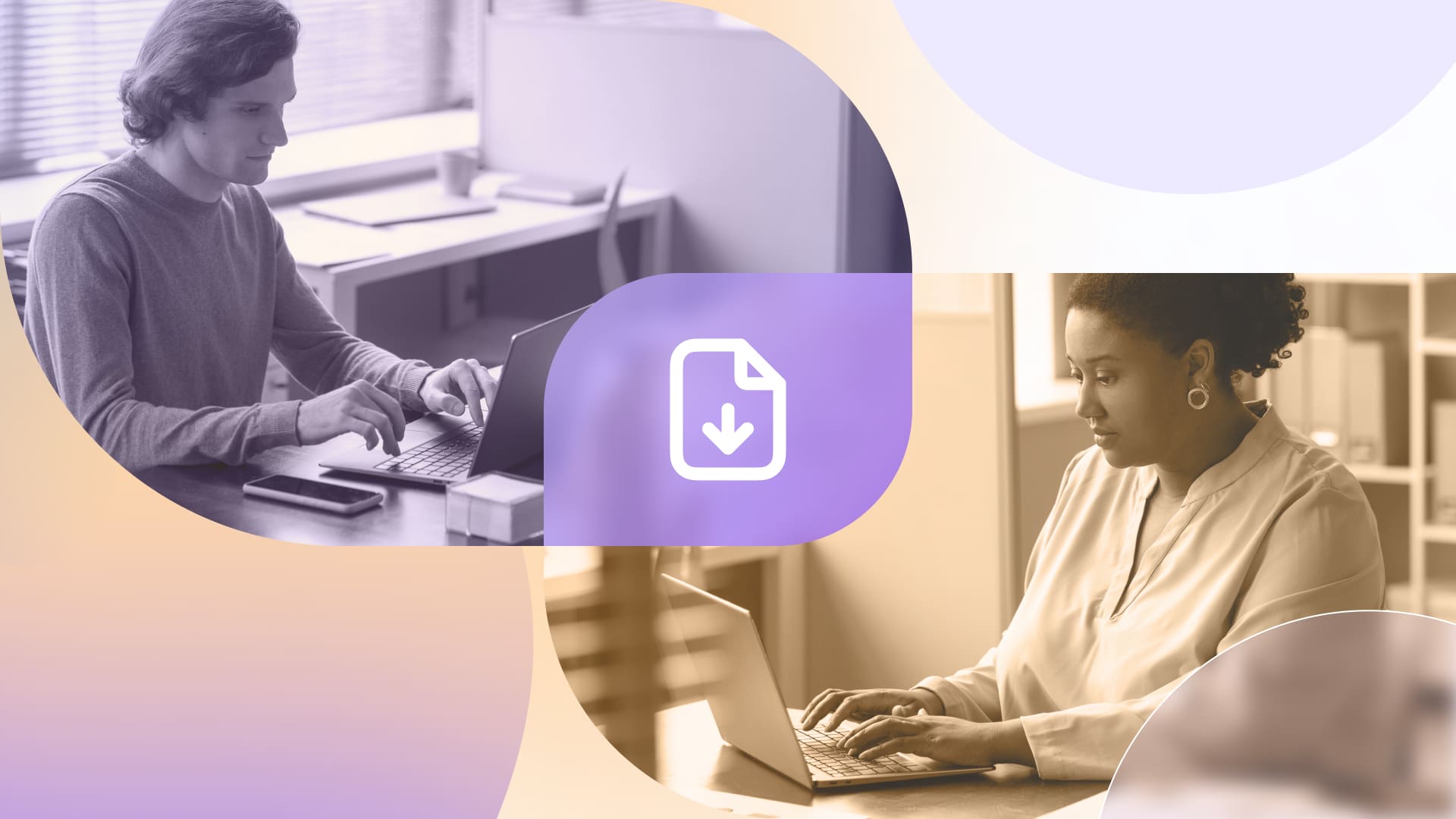
Key components of IT support in manufacturing
Manufacturing environments rely on a mix of industrial hardware, specialized software, and interconnected systems to maintain efficiency. IT support plays a central role in keeping these elements functional, secure, and up-to-date.
Unlike standard office IT, manufacturing IT must account for legacy systems, real-time production monitoring, and automation, making reliability and cybersecurity even more critical. Let's review this in more detail.
#1: Hardware and Infrastructure Management
Manufacturing facilities often rely on a mix of legacy systems, modern machinery, and IoT (Internet of Things) devices. IT support ensures that these components communicate effectively, remain operational, and are regularly updated or replaced as needed. For example, supporting CNC machines or smart factory setups requires robust IT infrastructure.
#2: Software and system maintenance
These enterprises use specialized software such as Manufacturing Enterprise Resource Planning (ERP) systems, Computer-Aided Design (CAD) software, and Manufacturing Execution Systems (MES). IT support involves installing, updating, and troubleshooting these tools to ensure they perform optimally.
#3: Cybersecurity and data protection
Manufacturing is increasingly targeted by cyberattacks. IT support ensures that sensitive production data, intellectual property, and customer information are safeguarded with measures like firewalls, encryption, and regular vulnerability assessments.
#4: Network connectivity and troubleshooting
In smart factories, uninterrupted connectivity between devices is essential for real-time monitoring and automation. IT support maintains the network infrastructure, resolves connectivity issues, and ensures data flows seamlessly across systems.
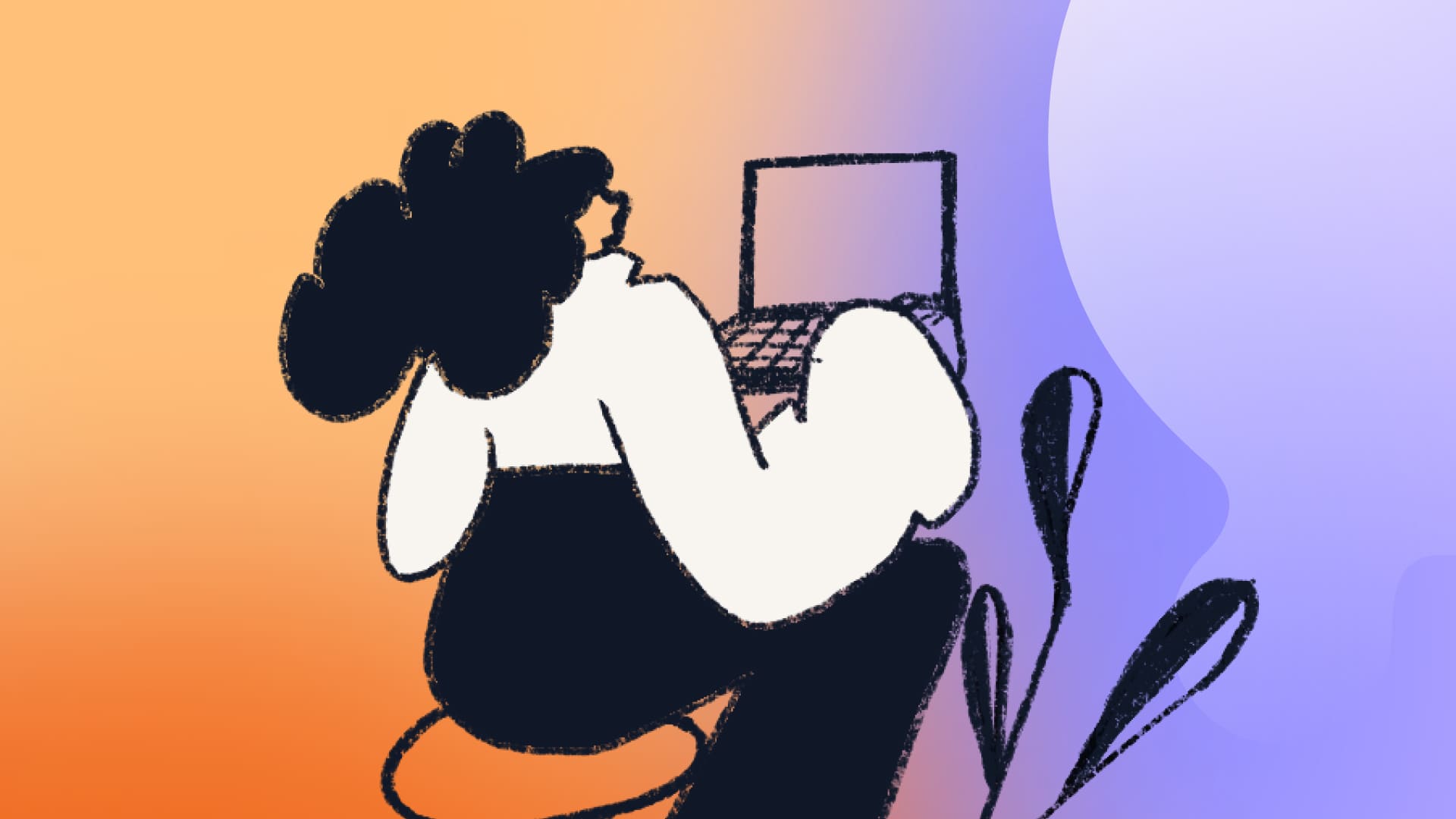
Examples of IT support for manufacturing companies in action
Here are three examples of IT support in action. These illustrate why it’s so important for this particular industry to have IT support, whether it’s coming from a dedicated IT department or a third party.
- A production line suddenly stops due to a software glitch in the MES system. IT support teams step in to identify the root cause, apply a patch or reconfigure the system, and get operations running again, minimizing downtime.
- A manufacturing plant adopts IoT-enabled devices to monitor equipment performance. IT support ensures these devices are integrated into the broader network, regularly updated, and securely connected to prevent unauthorized access.
- An ERP system experiences performance lags during a critical supply chain process. IT support optimizes the software or adjusts server resources to restore efficiency.
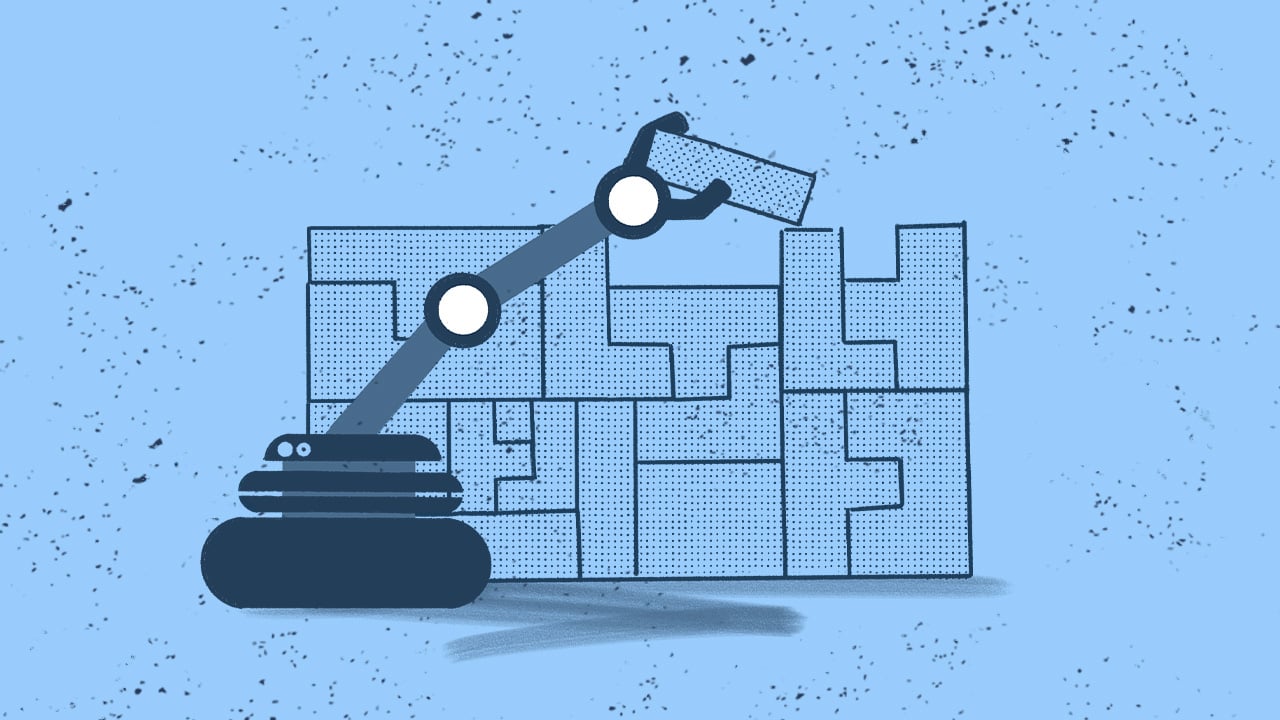
7 reasons why the manufacturing industry will benefit from IT support
Here are 7 key reasons why IT support is a game-changer for the manufacturing sector:
1. It minimized downtime:
Unplanned downtime can cost manufacturers thousands of dollars per minute. IT support ensures that systems remain operational by proactively monitoring for potential issues, performing regular maintenance, and resolving problems quickly when they arise.
2. Enhancing cybersecurity:
The rising connectivity and integration of IT and operational technology (OT) systems have expanded vulnerabilities for manufacturing companies, now prime targets for cyberattacks.
In 2024, the manufacturing industry experienced 394 unique ransomware attacks from July to September, accounting for 71% of all ransomware incidents across key industries during that period. There's been a shift from traditional financial extortion to operational sabotage.
IT support ensures robust cybersecurity measures are in place, such as firewalls, encrypted communication, and regular vulnerability testing, safeguarding valuable intellectual property and operational data.
3. Streamlining Supply Chain Management
Manufacturing relies heavily on complex supply chains, and any disruptions can cascade into significant delays. IT support helps maintain ERP systems, which are vital for tracking inventory, managing orders, and coordinating with suppliers, ensuring a seamless flow of goods and materials.
4. Enabling smart manufacturing and IoT integration
The rise of smart manufacturing has transformed the industry, with IoT devices monitoring equipment, tracking production, and providing real-time insights. IT support facilitates the integration and maintenance of these technologies, ensuring they function effectively and securely.
5. Supporting compliance with industry regulations
Strict standards and regulations, such as ISO certifications and environmental requirements, govern manufacturing. IT support assists in maintaining accurate records, automating compliance processes, and generating the necessary reports to meet these standards.
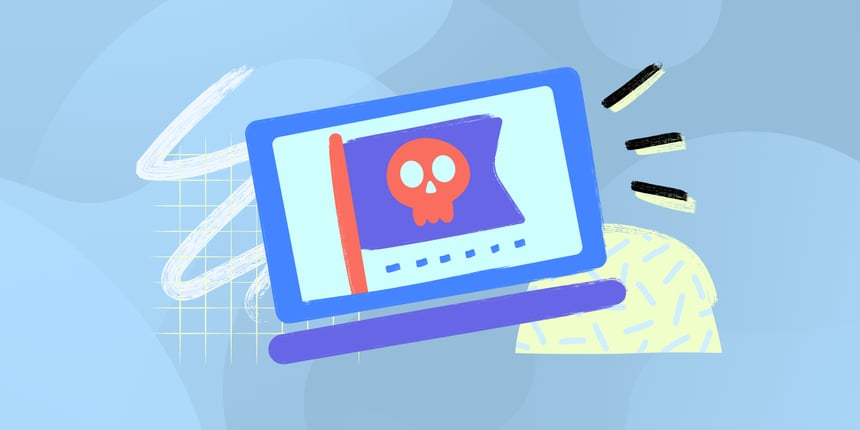
How to choose the right tool for manufacturing IT support
Manufacturing IT support covers a wide range of processes. Support teams need solutions that help them:
- Respond to incidents and service requests
- Manage system maintenance and updates
- Monitor network performance and connectivity
- Ensure cybersecurity and compliance
For these core needs, an IT Service Management (ITSM) solution is essential. ITSM provides a structured approach to handling IT incidents, service requests, and system maintenance. A well-implemented ITSM tool helps manufacturing IT teams:
- Automate and prioritize support tickets for faster issue resolution.
- Set up workflows that align with production schedules and operational needs.
- Track and report on IT performance to improve long-term support strategies.
In addition to ITSM, IT Asset Management (ITAM) tools can enhance IT support by keeping track of hardware, software, and infrastructure. While ITSM focuses on resolving IT issues, ITAM helps prevent them by:
- Monitoring asset health and performance to reduce unexpected failures.
- Automating software updates and compliance reporting.
- Providing visibility into IT inventory to oversee and optimize resource use.
InvGate Service Management is a centralized platform to manage and resolve IT incidents and requests efficiently. Its customizable workflows and built-in reporting tools help streamline IT support processes, ensuring faster resolution times and better alignment with manufacturing operations. Features like automated ticketing, self-service portals, and real-time tracking are especially useful in maintaining the uptime and reliability that manufacturing demands.
For organizations looking to strengthen their IT asset oversight, InvGate Asset Management adds full visibility into hardware and software assets. It helps automate reporting to ensure compliance and seamlessly manage IT infrastructure.
With its intuitive interface and extensive capabilities, InvGate can adapt to both outsourced and in-house IT support strategies.
To sum up
IT support is no longer optional for the manufacturing industry —it’s a necessity. Whether you outsource for flexibility and expertise or build an in-house team for control and alignment, the key is choosing the right approach for your business needs.
With the right IT support system in place, your manufacturing business is primed for efficiency, innovation, and growth.
Frequently Asked Questions
1. What is the role of IT in manufacturing?
IT plays a critical role in streamlining processes, improving efficiency, and enabling innovation in manufacturing. It supports everything from managing production systems and supply chains to ensuring data security and integrating advanced technologies like IoT and automation.
2. How does IT help in manufacturing?
IT helps manufacturers by automating processes, optimizing production workflows, and reducing downtime. It also improves decision-making through data analysis, enhances communication across departments, and safeguards sensitive information with robust cybersecurity measures.
3. What is included in IT support?
IT support in manufacturing typically includes hardware and software maintenance, network connectivity, cybersecurity, system troubleshooting, and support for specialized tools like ERP systems or IoT devices. It ensures the smooth functioning of technology critical to production.
4. What technology is used in manufacturing?
Manufacturing relies on technologies such as IoT, AI, robotics, ERP systems, Manufacturing Execution Systems (MES), CAD software, and data analytics platforms. These tools enable smart manufacturing, real-time monitoring, and seamless integration of operations.