Mobile Device Inventory Management (MDIM) is the solution to a common IT headache: spending hours every week hunting down lost or outdated mobile devices. Sound familiar? You’re not alone.
However, by implementing MDIM, organizations can tackle these type of challenges head-on and transform the way they manage their mobile assets. The truth is that managing mobile devices effectively isn't just a nice-to-have—it's a must-have for businesses to stay secure and efficient.
This blog post explores what Mobile Device Inventory Management is, its benefits, how it works, and the best practices to help your team thrive. By the end, you'll have a clear roadmap for managing the chaos of mobile devices while ensuring security and efficiency.
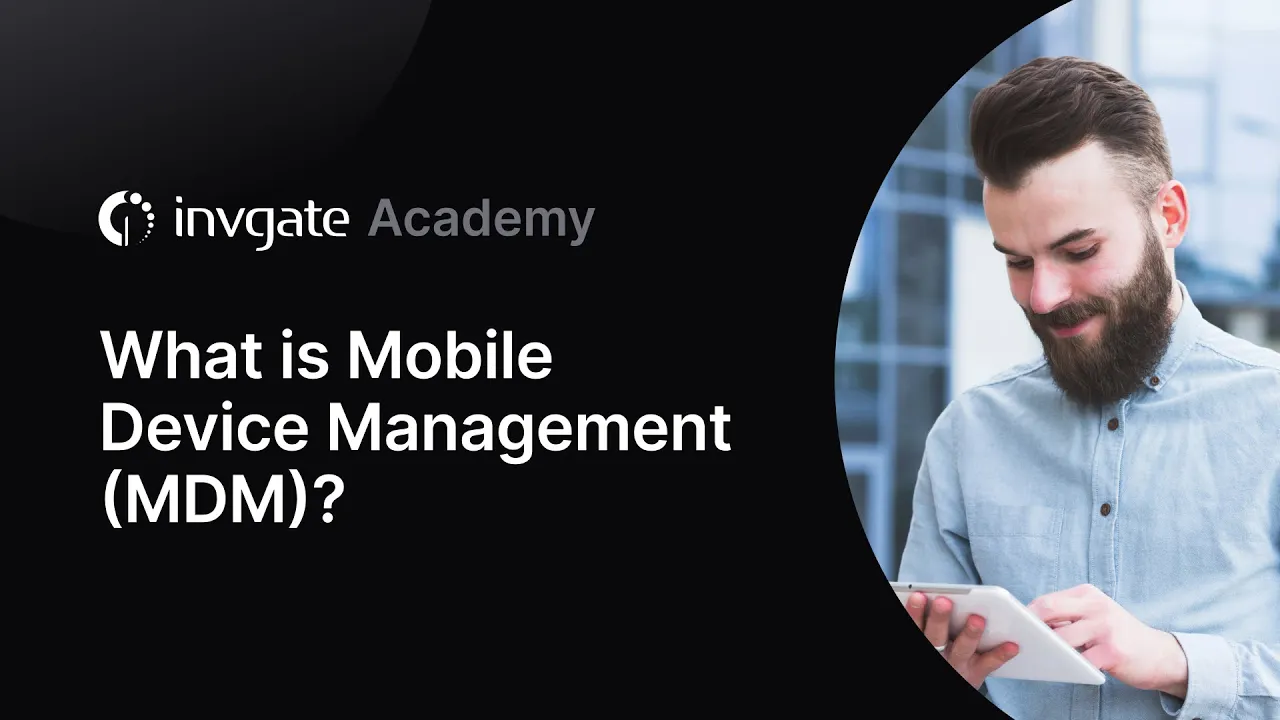
What is Mobile Device Inventory Management?
In a nutshell, Mobile Device Inventory Management refers to the process of tracking, monitoring, and managing mobile devices within an organization. This includes smartphones, tablets, laptops, and other portable devices that employees use to access corporate resources.
The primary goal of MDIM is to ensure that all devices are secure, properly configured, and accounted for throughout their lifecycle. This involves features like real-time tracking, automated updates, and centralized inventory systems that may require collaboration with a mobile applications development team to create custom management solutions and optimize Device Management.
What is the difference with Device Inventory Management (DIM)?
Although they are closely related, there are significant differences between MDIM and Device Inventory Management (DIM). MDIM focuses specifically on mobile devices such as smartphones, tablets, and laptops. It includes features like tracking device details, app usage, and security controls such as remote wipe and encryption, catering to the unique challenges of managing portable and remote devices.
DIM, on the other hand, covers a broader range of IT assets, including desktops, servers, IoT devices, and peripherals. It emphasizes general IT Asset Management tasks such as lifecycle tracking and compliance, offering a comprehensive overview of the entire IT environment without the specialized mobile-focused tools provided by MDIM.
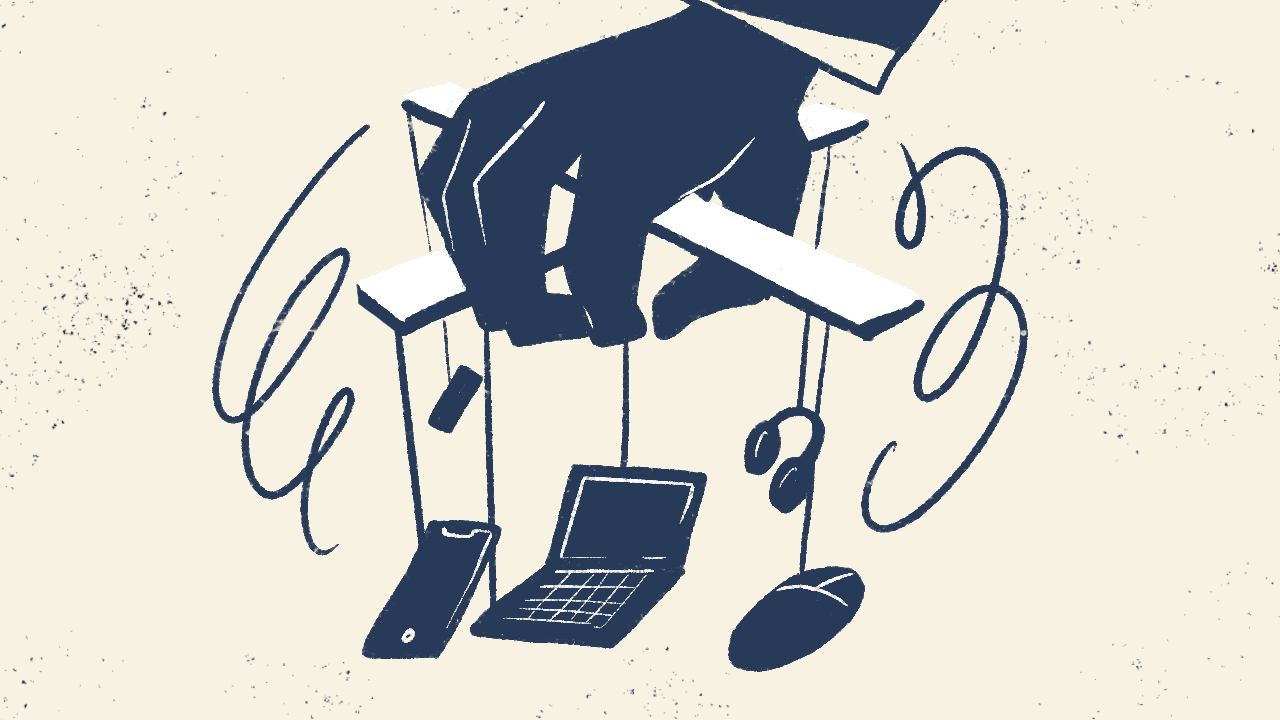
Benefits of Mobile Device Inventory Management
1. Enhanced efficiency through automation
Mobile Device Inventory Management streamlines inventory tracking by replacing manual data entry with automated processes via Inventory Management software and inventory apps. This ensures faster, more accurate Inventory Management tasks, reducing human error and saving time. The use of real-time inventory data allows businesses to respond quickly to changes in stock levels or asset availability.
Additionally, integration with cloud software ensures all devices are managed on a single platform. Whether using native mobile apps or web-based software, employees can access an up-to-date inventory database, improving collaboration between warehouse personnel and office staff.
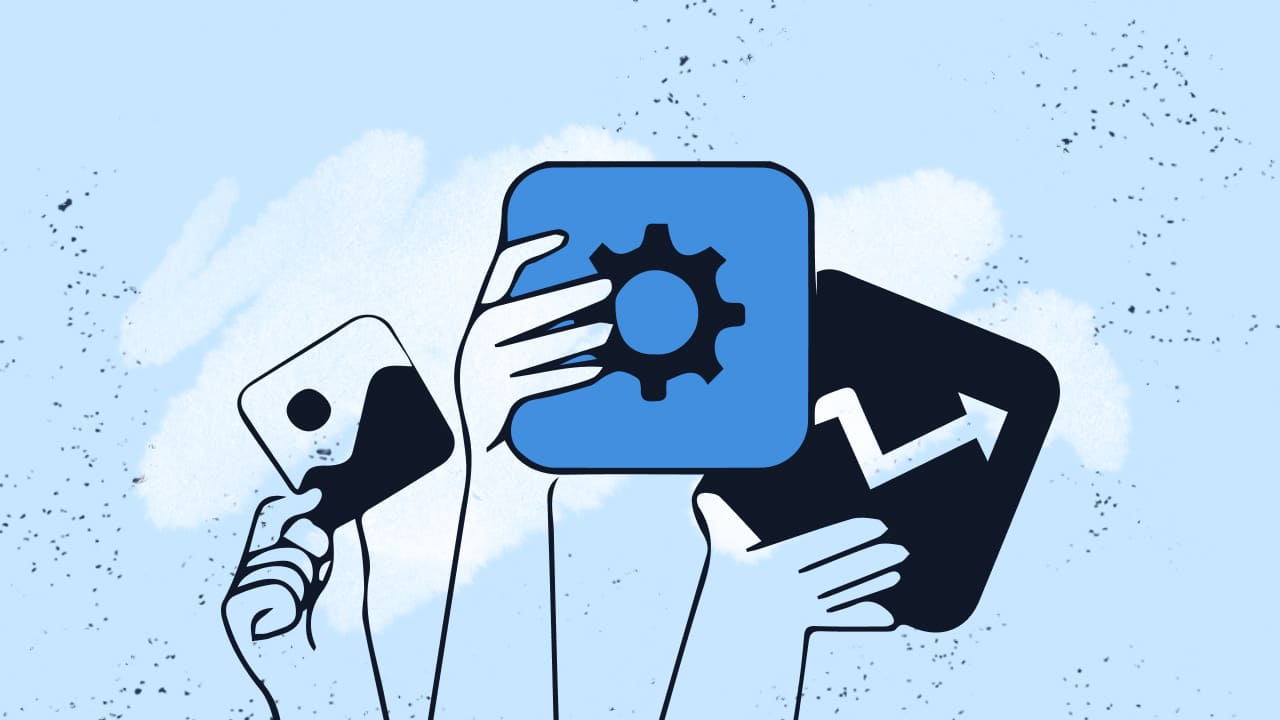
2. Improved security and compliance
Mobile Device Inventory Management helps organizations maintain security and compliance by tracking devices throughout their lifecycle. Features like visual documentation, user accounts, and secure access controls ensure all devices are accounted for and used appropriately.
These systems integrate with existing operating systems and cloud software to centralize control, enhancing data security. This not only protects business operations but also ensures compliance with organizational policies and regulations.
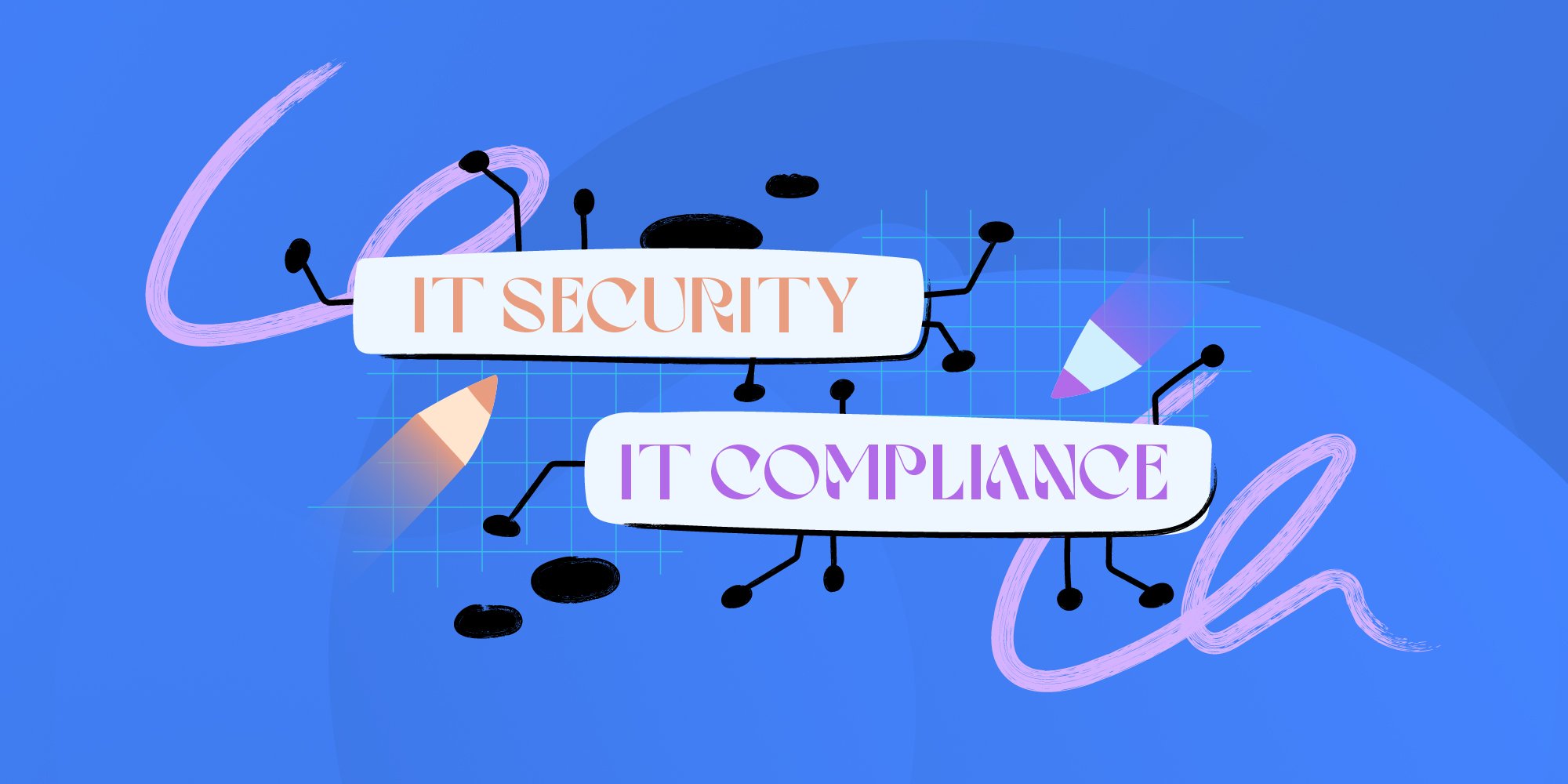
3. Cost savings and resource optimization
Mobile Device Inventory Management reduces operational costs by providing real-time visibility into device usage, maintenance schedules, and lifecycle status. This allows organizations to optimize resource allocation, ensuring that underutilized devices are redeployed and outdated or unnecessary assets are decommissioned.
With centralized data accessible via mobile apps or cloud-based systems, businesses can identify trends like frequent repairs or replacements, helping to budget more effectively and prevent unexpected expenses. By reducing wastage and improving asset utilization, companies can maximize the return on their IT investments.
How does Mobile Device Inventory Management work?
Mobile Device Inventory Management involves a systematic process that ensures all devices are effectively tracked, managed, and optimized for business operations. Below are the key steps, from setup to achieving seamless management.
1. Setting up the Inventory Management system
The process begins with selecting the right Inventory Management software or a even a dedicated Mobile Inventory Management solution. Businesses need to choose tools that align with their needs, such as native mobile apps, cloud software, or web-based software. Once selected, the system is configured to integrate with the organization's existing software, such as asset databases or operating systems.
During this phase, businesses define key parameters, such as user accounts, device categories, and security settings. The system is also equipped with cloud connectivity to ensure all devices can be tracked in real time, regardless of location.
2. Adding and categorizing devices
The next step is importing device details into the inventory database. This includes registering all mobile devices, such as smartphones, tablets, and laptops, along with their specifications (e.g., operating system, serial numbers, and SIM details). This information is entered manually or using tools like QR code scanning for faster input.
Devices are then categorized based on criteria like department, usage, or ownership (e.g., company-owned vs. BYOD). This categorization streamlines Inventory Management tasks and ensures that every device is easily identifiable in the system.

3. Real-time data collection and tracking
Once devices are added, the system begins tracking them in real time. This is achieved through mobile apps or cloud software that continuously monitor device usage, location, and status. Data is automatically synced to a central platform, eliminating manual data entry and ensuring accuracy.
The system also tracks inventory updates, such as when devices are added, reassigned, or decommissioned. This allows businesses to maintain an up-to-date inventory and avoid discrepancies.
4. Automating tasks and enhancing visibility
MDIM works best when routine tasks are automated. This includes generating alerts for stock shortages, scheduling maintenance, and ensuring compliance with policies. Automation reduces time spent on manual tasks, allowing businesses to focus on higher-value activities.
Enhanced visibility is achieved through mobile-optimized web pages or smartphone apps that provide a comprehensive overview of stock levels, device conditions, and usage trends. This visibility ensures all stakeholders have access to the same real-time information.
5. Reporting, analysis, and optimization
The final step involves using the system’s reporting and analytics features to evaluate performance. Businesses can generate reports on stock levels, device lifecycles, and compliance metrics. These insights enable demand forecasting, identifying inefficiencies, and optimizing Inventory Management processes.
Over time, the system becomes a key tool for improving productivity and reducing costs. By automating tasks, providing real-time data, and ensuring all devices are accounted for, businesses achieve effective Inventory Management and better overall operations.

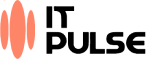
Mobile Device Inventory Management best practices
1. Implement a centralized inventory system
Using a centralized inventory system is one of the most effective ways to streamline Mobile Device Inventory Management. By consolidating data for all the devices into a single platform, businesses can ensure consistency and improve efficiency. This approach eliminates discrepancies caused by scattered records and allows for seamless updates across departments.
A centralized system also integrates with back end cloud software, ensuring real-time data access for office employees and remote workers alike. With a single source of truth, organizations can manage inventory levels more effectively, improving decision-making and reducing the time previously spent reconciling manual records.
2. Leverage real-time data access
Ensuring real-time data access is critical for maintaining accurate inventory records. Using Mobile Inventory Management software or a mobile inventory app, businesses can track devices instantly and make adjustments as needed. This eliminates delays caused by outdated information and enables businesses to respond quickly to changes in inventory levels.
Real-time access also helps identify security risks and inefficiencies, providing valuable insights into usage patterns and stock levels. By distributing real-time data to relevant stakeholders, companies can align their operations with up-to-date information, avoiding errors and improving overall productivity.
3. Define clear user permissions
Establishing clear user roles and permissions enhances both security and accountability. Assigning specific access rights ensures that only authorized personnel can update inventory records, reducing the risk of errors or unauthorized changes.
Best practices include regularly auditing permissions, assigning roles based on job responsibilities, and integrating permissions with MDM tools to streamline access control across systems.
4. Use automation to improve efficiency
Automation is a cornerstone of effective Mobile Inventory Management. By automating routine tasks like inventory counts, updates, and alerts, businesses save time and reduce human error. Automation also enhances tracking accuracy by integrating with Inventory Management software options that provide real-time updates.
For example, alerts can notify users of low inventory levels or maintenance needs, enabling proactive management. This not only reduces the workload on employees but also ensures inventory records remain accurate and up-to-date without relying on manual intervention.
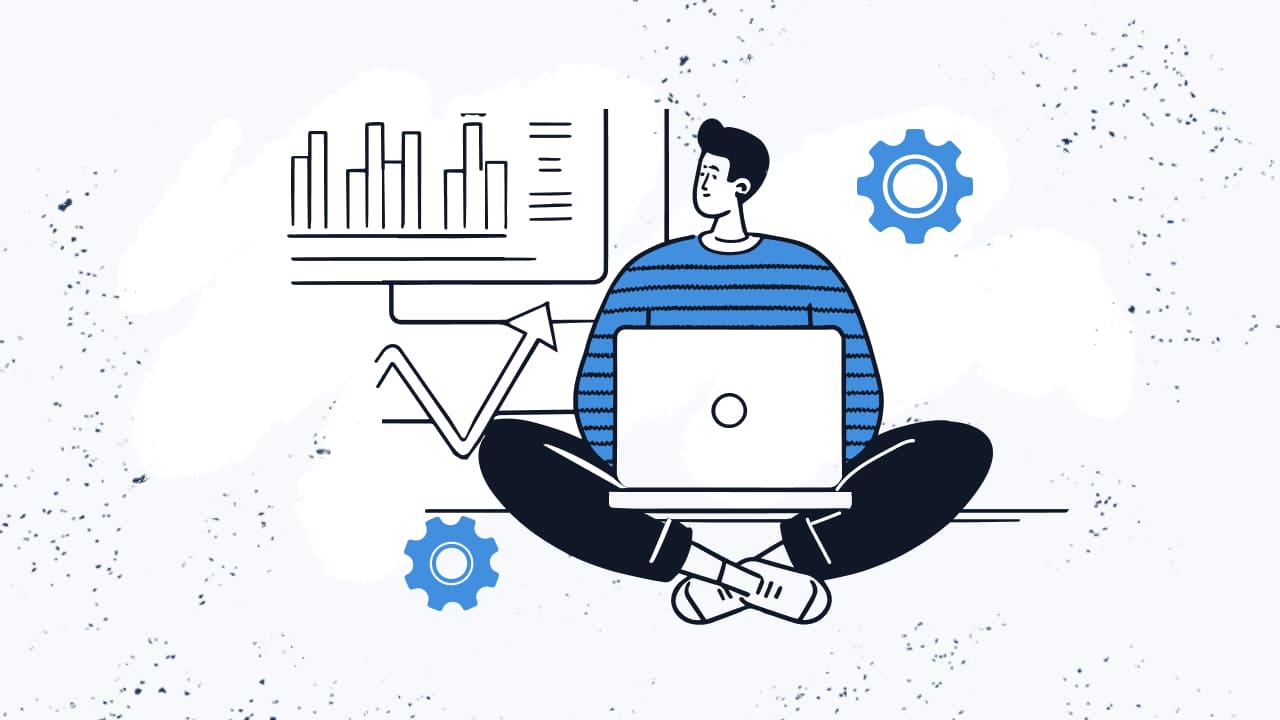
5. Assign unique identifiers to devices
Assigning unique identifiers like serial numbers, QR codes, or asset tags is a simple yet critical step in tracking devices. These identifiers can include details like owner, department, or purchase date, ensuring devices are easy to locate and verify during audits.
Unique identifiers can also be integrated with provisioning workflows provided by device OEMs, allowing seamless enrollment into MDM platforms and ensuring efficient tracking from deployment to decommissioning.
6. Conduct regular audits and reviews
Regular audits ensure the accuracy and completeness of your inventory. They help identify gaps, such as missing or non-compliant devices, and provide opportunities to address excess or underutilized assets.
Audits should also focus on device performance, security, and lifecycle status, offering actionable insights to improve overall management. Combining manual audits with MDM-generated reports enhances reliability and efficiency.
7. Optimize mobile device costs
Tracking mobile devices isn’t just about inventory—it’s also about cost optimization. MDM solutions can help monitor data usage, avoid overages, and identify underutilized devices.
Negotiate vendor contracts, recycle old devices, and use analytics to benchmark spending against industry standards. This approach aligns costs with business goals and ensures a higher return on investment.
8. Prioritize seamless integration
Choosing Mobile Inventory Management software with seamless integration capabilities is essential for streamlining processes. Ensure the system works well with existing tools, such as Asset Management platforms or traditional hardware like scanners and tablets. Integration reduces the need for duplicate data entry and ensures smooth workflows.
A system with a user-friendly interface also improves adoption rates among employees, enabling businesses to transition smoothly to their inventory management system. This integration is key to leveraging all the features of the software and maximizing its impact on operations.
Mobile Device Inventory Management software
What is a Mobile Device Inventory Management software? Well, it's a specialized tool designed to streamline the tracking, management, and maintenance of mobile devices within an organization. This type of software often provides a centralized platform to manage smartphones, tablets, laptops, and other portable devices, ensuring they are accounted for, secure, and optimized for business use.
Key features include real-time data access, device lifecycle tracking, and remote management capabilities, such as app control and security enforcement. By using this software, businesses can automate Inventory Management tasks, eliminate manual data entry, and reduce security risks, enabling a more efficient and secure approach to managing their mobile assets. With seamless integration into existing systems, it helps organizations maintain accurate inventory records and ensures all devices are compliant with company policies.
Final thoughts
Mobile Device Inventory Management is no longer a luxury—it’s a necessity for organizations looking to stay efficient, secure, and competitive in today’s fast-paced environment. By implementing MDIM, businesses can overcome common challenges such as device mismanagement, outdated records, and security vulnerabilities, while simultaneously improving productivity and reducing costs.
Whether you’re just beginning to explore Inventory Management or seeking to optimize an existing system, understanding the benefits, processes, and best practices of MDIM is essential. From automating routine tasks to leveraging real-time data and integrating seamlessly with existing tools, MDIM empowers businesses to stay ahead. With the right approach, managing mobile devices can transform from a time-consuming burden into a streamlined, effective operation that supports your organization’s goals.